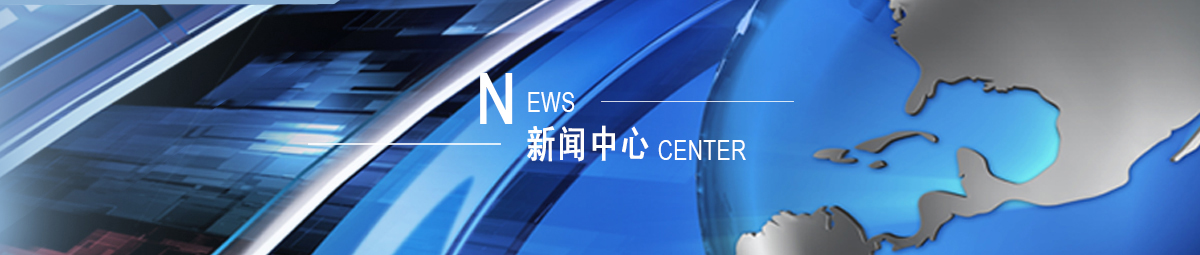
公司新闻
如何降低LNG加气站气损?人员操作是关键!
发布时间2019-07-02 浏览次数:253
很多加气站都曾经遇到过卸车卸不干净的情况,导致卸车结束后,卸车量与装车单相比有超过200kg的磅差。本文总结了“老司机”的一些经验,并探索了从人工操作优化方面解决这个行业难题。
造成原因:
一是卸车操作不得当,卸车需要将槽车压力增压到高于储罐压力时才能进行,但储罐经过一段运行时一般压力较高,通常能达到0.8MPA以上,而槽车压力一般较低,约为0.2MPA左右甚至更低,如果直接对槽车增压、且对储罐排放将会增加大量排放。另外卸车完毕后槽车压力直接排出,或与储罐上进液进行压力平衡,使槽车泄压不到位。造成卸车损失,另外如卸车过程中泵的频率过高,在卸车后期时容易造成泵池进出液流量不平衡,引起泵池排空。
二是加气完成的系统处理,加气完成后,泵会停止运行,这时候,泵池及管道中会有许多残留液体,这部分液体气化速度相当快,基本通过泵后回流管回到储罐的气相空间,造成储罐压力快速上升,被迫排空储罐。 三是加气频率过高,储罐压力有比较高时会造成加液压力过高,导致加液安全阀起跳从而造成气损。
四是防控管理不严格。储罐压力达到排放压力需进行放空时,操作人员不严格监控,压力降到正常值时不及时关闭放空阀,造成浪费。
解决方案:
一是卸车时必须平压,而且平压操作时,必须使储罐气相与槽车液相连接平衡压力,气体进入槽车时可以液化平压完成后,储罐会稳定在一个较低压力值上。严格执行采用储罐气相气体对卸车管线进行置换三遍的方式。
二是卸车后期,在槽车内LNG卸完时,通过倒阀门,储罐进液方式由上进液改为下进液,把槽车内的BOG卸至储罐,此方法可以使槽车的压力降至0.3MPA上下,可以减少卸车损耗约80KG。
三是合理安排进液计划,杜出现三个站及以上数量的加气站合卸一车的情况出现。
四是卸车后期根据泵池的进液情况,将潜液泵频率调整到80HZ左右,降低潜液泵出液流量,来保持泵池的进出液流量平衡。
五是在液温较低而储罐压力又较高时进行液-泵-上进液的打循环操作,使气相空间部分气体降温再液化,以此达到降低储罐压力的目的,减少排放次数
六是定期检查加液控制阀是否内漏,检查方法为空枪加液如显示屏显示有加液量可判定为阀门内漏需更换阀门主垫片或阀芯。加液时如果加气控制阀在未起跳时加气软管会有吱吱的声音,也可判定为内漏。
七是在放空时,放空阀需缓慢开启,现场必须留人看守,压力降至正常值时及时关闭放空阀。
(本文内容来源于网络,如有侵权请联系删除)